Resin Coated Quartz Sand
We are one among the leading manufacturers of Resin Coated Quartz Sand based at Hyderabad & incepted in the year 2009. We own Quartz Crushing Unit. Our current production capacities are 2000 MT of crushing and 1200 MT of Resin Coating. Resin Coated Quartz Sand is used in the production of moulds and cores making process mainly in water jackets of cylinder blocks & Heads. The company is led by Mr. K.Raghava Reddy as Managing Director & K.Srujana Reddy as Director who has vast experience in the field.
SHELL SAND – Q
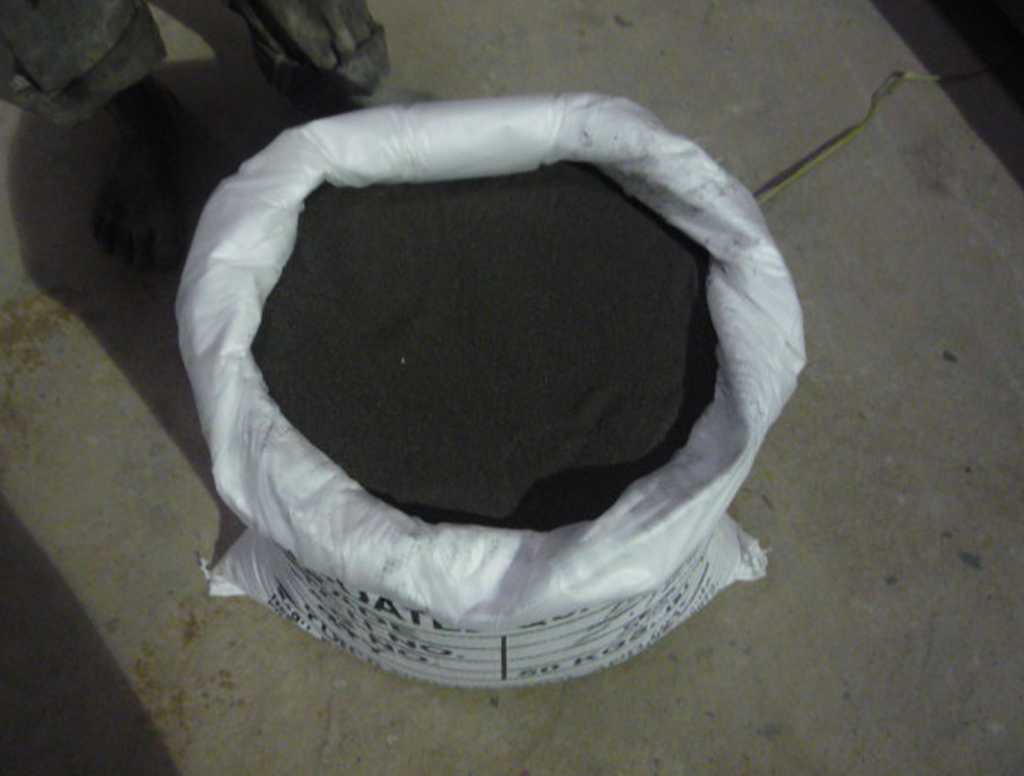
A superior grade Resin Coated Quartz Sand for Shell Moulding /Core making process
General descriptionSHELL SAND – Q is a Resin Coated Quartz Sand for use in the production of moulds and cores to produce castings by shell process. This is a high refractory and purity Sand with Silica content more than 98%. It is free from clay and dust and reduces the gas defects.
PurposeThe Resin Coated Sand is one of the most widely used repetitive mould and core making processes mainly for water jackets of cylinder blocks and Heads. In this process Resin Coated Sand is used for making moulds by dump box method and cores by shooting. The free flowing Resin Coated Sand is cured in the core boxes heated to temperaturse of 230-250 deg. C to form the desired shapes.
SHELL SAND – Q is a Resin Coated quartz Sand taken from quartz mines near Hyderabad. This Sand gives high tensile strength and low gas content. It exhibits high refractoryness low deformation. The quartz Sand Coated with Shell Resin is also more flowable and has greater resistance to peelback and lumping-up on storage.
BENEFITS- SHELL SAND – Q made with low viscosity Resin which helps in easy and homogenous mixing in the coating process. This leads to a uniformly Coated Sand and hence consistent performance to produce strong moulds and cores. This reduces casting rejections due to inclusions, erosion and gas defects.
- SHELL SAND – Q is a highly reactive and faster curing as we use HSLD grade Resin which leads to lower hot air cycle time during coating process and a shorter curing time during core and mould making process. This helps in increasing the productivity.
- SHELL SAND – Q gives higher strengths than conventional Sands. Hence, lower addition rates of the Resin are possible to get the required strengths which gives lower gas content.
- SHELL SAND – Q has a very good resistance to lumping and therefore core shooting is made easier to produce well compacted cores.
- SHELL SAND – Q has a excellent resistance to peelback. This ensures that stronger and thicker shells are produced. As a result problems of shell puncture will be greatly reduced.
- The gas content of SHELL SAND – Q is low. This leads to production of castings with minimum risk of blow holes and porosity.
- SHELL SAND - Q is best suitable for moulds of cylinder Heads and cores of water jackets
- Charge the Sand in Sand dry hopper of core or mould shooter.
- Keep the core or mould box clean and heat upto temp of 230 to 250 deg C.
- Shoot the core or mould at specified temperature and cycle time.
- Ejected cores should be stored in cool and dry place.
Sand | Quartz Sand of AFS No.60-65 |
Pattern temperature | 230oC |
Curing Time | 2 – 3 minutes |
Hot tensile strength | 450 – 460 psi |
Stick point | 98 – 102oC |
Transverse strength | 75 kgs/sq cm |
SHELL SAND – Q has a shelf life of 6 months when stored at ambient temperature of 30 deg C without exposure to sun.
Standard PackingSHELL SAND – Q: 50 kg in HDPE bags
Address
SMARCO Industries Pvt. Ltd
Srilakshmi heights, plot no.700
flat no. 102, Mathrusri nagar
Miyapur,Hyderabad- 500050.
Mob.No: +91 9989 3792 22
Enquiries:
Email: mktg@smarco.in
krreddy@smarco.in